Maximizing Safety and Efficiency in Your Business and Garden Operations with Expert LOLER Inspection
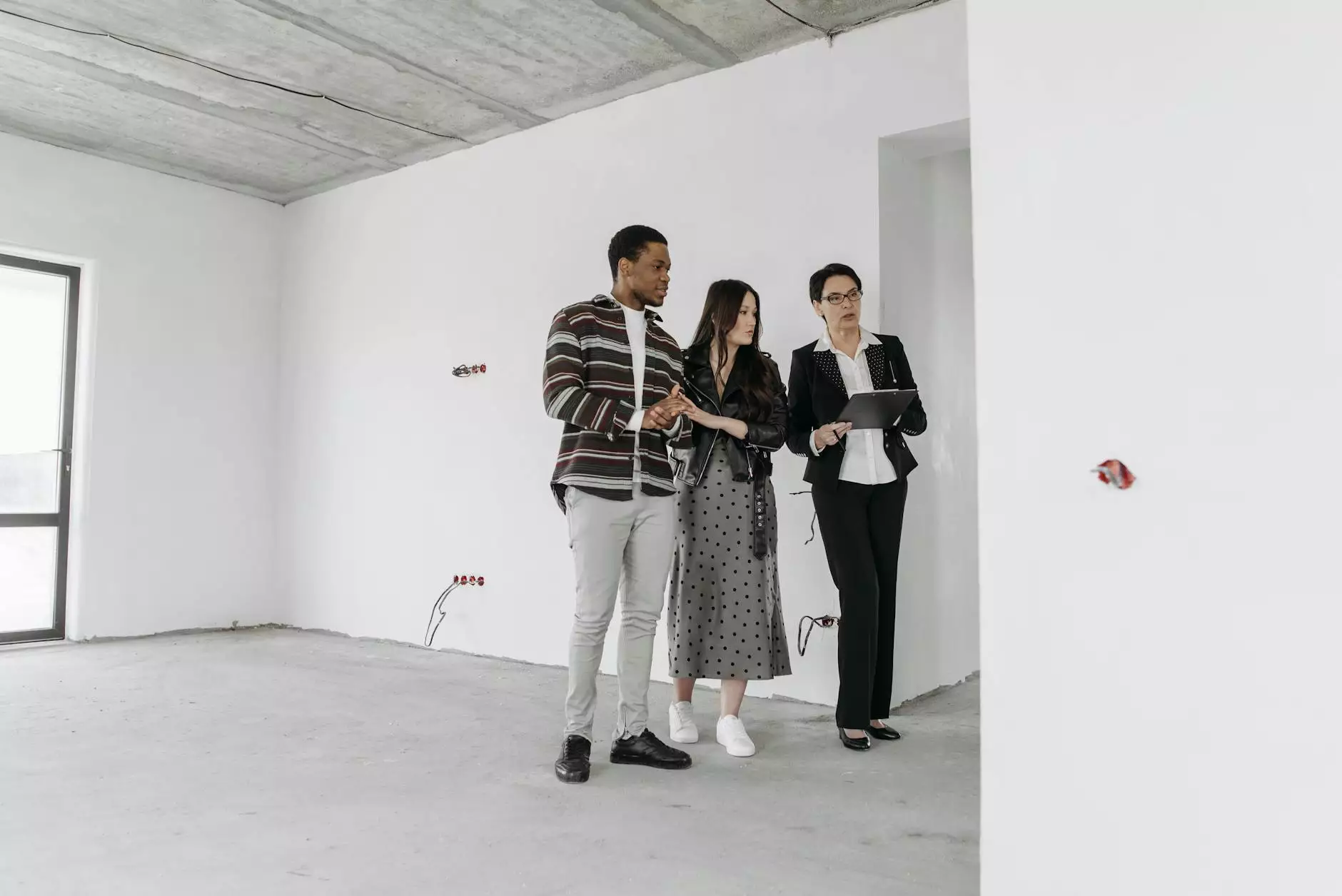
Ensuring safety and compliance is a fundamental aspect of managing a successful business, especially within sectors like Home & Garden, Gardeners, and Pest Control. One of the most critical safety protocols is the LOLER inspection, a vital safety check that underpins safe lifting operations and mechanical equipment management.
Understanding the Significance of LOLER Inspection in Business Operations
The abbreviation LOLER stands for Lifting Operations and Lifting Equipment Regulations. These regulations, introduced by the UK Government, aim to prevent accidents and ensure the safety of workers and the public when using lifting equipment in various industries—including gardening, pest control, and general business environments.
In practical terms, a loler inspection is a comprehensive safety assessment of all lifting devices, such as cranes, hoists, lifts, slings, and other mechanical tools involved in lifting operations. Regular inspections are not only a legal requirement but also a crucial step toward safeguarding your team, clients, and assets.
Why Regular LOLER Inspections Are Critical for Your Business and Garden Operations
Implementing regular loler inspection schedules offers numerous advantages that extend beyond compliance:
- Enhanced Safety: Detects potential faults before they result in accidents or injuries, creating a safer work environment.
- Legal Compliance: Ensures adherence to UK safety regulations, avoiding costly fines and legal consequences.
- Operational Efficiency: Maintains the reliability of lifting equipment, reducing downtime and increasing productivity.
- Cost Savings: Prevents expensive repairs and equipment failures through early defect detection.
- Reputation Management: Demonstrates your commitment to safety and quality, which enhances your business credibility.
Components of a Thorough LOLER Inspection
An effective loler inspection covers detailed assessments of all relevant equipment components, including:
- Structural Integrity: Checking for cracks, deformities, or corrosion in the framework.
- Mechanical Systems: Evaluating gears, pulleys, brakes, and motors for proper function.
- Hydraulic and Pneumatic Systems: Inspecting for leaks, pressure irregularities, and wear.
- Sling and Lifting Accessories: Ensuring slings, hooks, shackles, and other attachments are in excellent condition.
- Operational Controls: Verifying that all safety and control devices are functioning correctly.
Each inspection culminates in a detailed report, highlighting any issues and recommending corrective actions to ensure ongoing safety and compliance.
Legal Requirements and Industry Standards for LOLER Inspections
Under the LOLER regulations, all lifting equipment must be thoroughly examined by a competent person:
- Initial Inspection: Before first use.
- Periodic Inspections: At least every 6 or 12 months, depending on the equipment and usage.
- Post-Repair or Modification: Inspections after any significant repair or adjustment.
Failing to adhere to these scheduled inspections can lead to significant legal repercussions, including fines, enforcement notices, and potential shutdowns. Therefore, partnering with qualified LOLER inspection providers like SafePlantUK ensures your compliance and safety standards are always met.
The Role of Professional LOLER Inspection Services in Your Business
Reliable LOLER inspection services do more than just tick regulatory boxes; they provide peace of mind. Professional inspectors possess the expertise to identify hidden faults and potential hazards that can jeopardize safety and efficiency.
Partnering with reputable providers, such as SafePlantUK, guarantees:
- Highly Qualified Inspectors: Certified and experienced in current safety standards.
- Comprehensive Assessments: Including visual inspections, operational tests, and detailed reporting.
- Tailored Inspection Plans: Customized schedules aligned with your operational needs and equipment usage.
- Clear Certification: Issuance of official clearance certificates demonstrating compliance.
- Ongoing Support and Advice: Guidance on maintenance and safety best practices.
Integrating LOLER Inspection into Your Business and Garden Maintenance Routine
Incorporate LOLER inspections seamlessly into your routine maintenance protocols to promote a culture of safety. Steps include:
- Scheduling Regular Inspections: Establish a calendar that aligns with legal requirements and operational demands.
- Training Your Staff: Educate your team about safe lifting practices and the importance of inspections.
- Maintaining Equipment Records: Keep detailed logs of inspections, repairs, and maintenance activities.
- Implementing Corrective Actions: Address any identified faults promptly to prevent accidents.
Proper integration ensures that safety is always prioritized, boosting overall productivity and reputation.
LOLER Inspection in the Context of Home & Garden, Gardeners, and Pest Control
While LOLER might typically be associated with industrial settings, its principles are equally critical for home garden projects and gardeners or pest control businesses. For instance:
- Garden Crane and Lift Equipment: Ensuring safety when using lifts or hoists during tree removal or heavy landscaping.
- Portable Lifting Devices: Regular inspections prevent accidents when lifting heavy objects or equipment in garden structures.
- Access Equipment: Such as scaffolds or elevated work platforms used during pest control or garden maintenance.
Implementing diligent LOLER inspection routines in these contexts elevates your business’s safety standards, minimizes liability, and demonstrates a professional approach that clients trust.
Choosing the Right LOLER Inspection Partner: Why SafePlantUK Is Your Best Choice
At SafePlantUK, we specialize in delivering comprehensive LOLER inspection services tailored to the unique needs of Home & Garden, Gardeners, and Pest Control industries. Our core advantages include:
- Expertise Across Multiple Sectors: Extensive experience in various fields requiring lifting equipment safety.
- Accredited and Certified Inspectors: Adherence to all industry standards and safety regulations.
- State-of-the-Art Inspection Techniques: Utilizing modern tools for precise assessments.
- Transparent Reporting and Documentation: Clear, detailed reports that satisfy regulatory compliance.
- Flexible Scheduling: Inspections that fit seamlessly into your operational timetable.
Conclusion: Elevate Your Business with Reliable LOLER Inspection Services
Ensuring safety is not just about compliance; it's a commitment to your team, your clients, and your reputation. LOLER inspection serves as the cornerstone of a proactive safety management system, preventing accidents, reducing costs, and maintaining operational excellence.
Don’t leave safety to chance—partner with industry leaders like SafePlantUK to implement comprehensive LOLER inspection protocols. Your business, employees, and clients will thank you for prioritizing safety, compliance, and quality in everything you do.