Understanding Plastic Molding: The Backbone of Modern Manufacturing
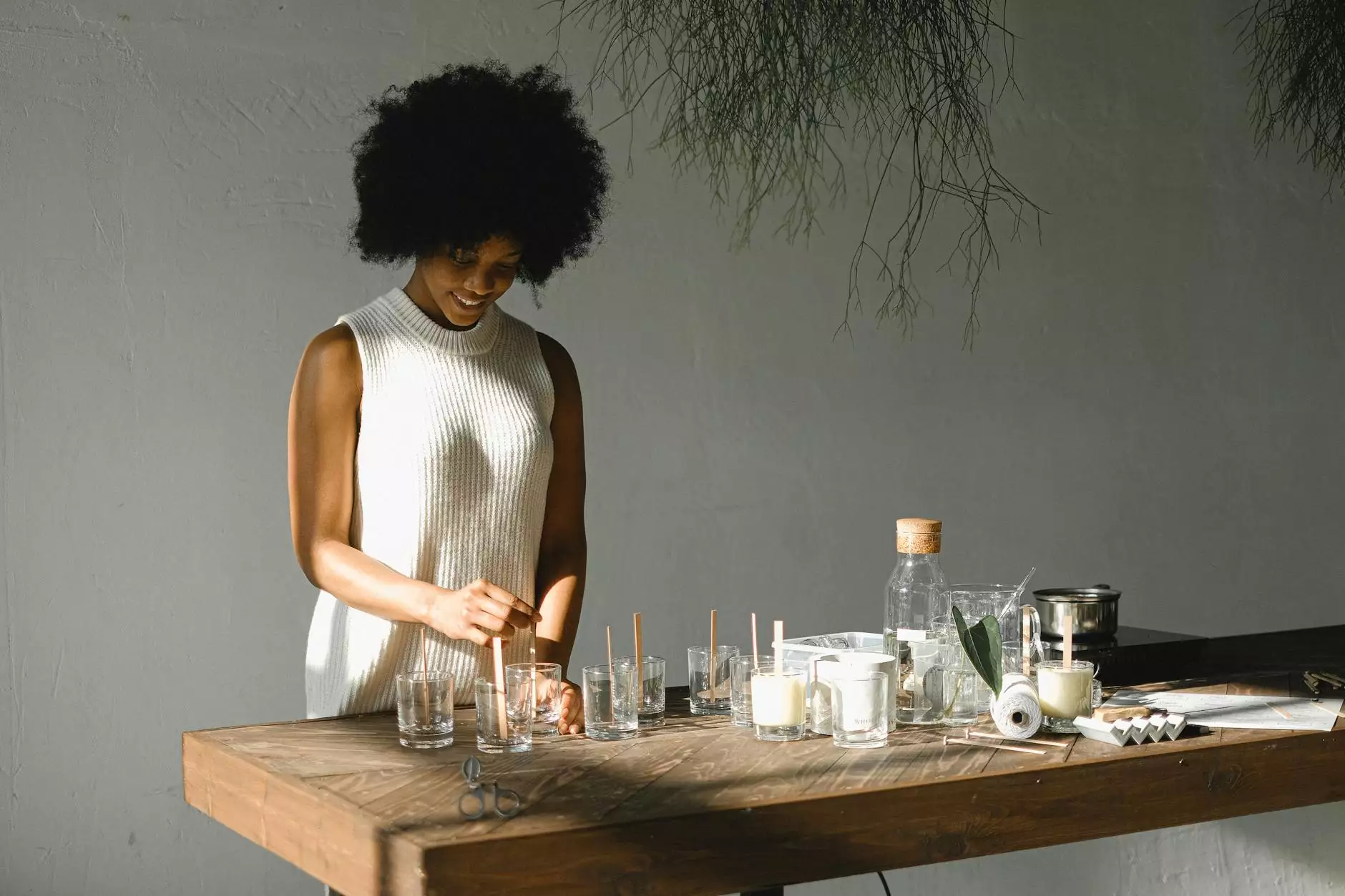
Plastic molding is a revolutionary process that has transformed the landscape of manufacturing. It allows for the rapid and efficient production of complex shapes and components, making it an essential technique for various industries. In this article, we will explore the different types of plastic molding, its significance in manufacturing, and the role it plays in enhancing productivity and efficiency.
What is Plastic Molding?
Plastic molding refers to a manufacturing process used to create parts by heating and shaping plastic materials in a mold. The process involves several stages, including material selection, heating, molding, and cooling. This method produces high volumes of identical pieces efficiently and cost-effectively.
The Importance of Plastic Molding in Various Industries
Plastic molding plays a pivotal role in various sectors, including:
- Automotive: Many car components are produced using plastic molding, which helps reduce weight and improve fuel efficiency.
- Consumer Goods: Household products, packaging, and personal care items are often manufactured through plastic molding.
- Electronics: This process is essential for creating durable and lightweight casings for electronic devices.
- Medical Devices: Numerous medical products, from syringes to surgical tools, rely on precision plastic molding for safety and performance.
Types of Plastic Molding Processes
There are several types of plastic molding processes, each with its unique advantages and applications:
1. Injection Molding
Injection molding is one of the most widely used plastic molding techniques. In this process, molten plastic is injected into a mold cavity, where it cools and solidifies into the desired shape. This method is ideal for high-volume production and can create intricate designs with excellent surface finishes.
2. Blow Molding
Blow molding is primarily used for producing hollow plastic parts, such as bottles and containers. In this method, air is blown into a molten plastic tube, causing it to expand and take the shape of the mold. This technique is highly efficient for packaging applications.
3. Rotational Molding
Rotational molding involves rotating a mold around two axes while it is heated. This process allows for the creation of large, hollow parts and is often used for products like kayaks and storage tanks. It offers excellent uniformity and wall thickness.
4. Compression Molding
Compression molding is a method where a heated plastic material is placed in an open mold. The mold is then closed and pressure is applied to shape the material. This technique is commonly used for thermosetting plastics and can produce strong, durable parts.
Advantages of Plastic Molding
The advantages of plastic molding are numerous, contributing to its popularity in manufacturing:
- Cost-Effective: High-volume production reduces the per-unit cost significantly, making it economical for mass manufacturing.
- Design Flexibility: Advanced molding techniques allow for complex shapes and designs, accommodating a wide range of applications.
- Material Versatility: A variety of plastic materials can be used, each offering unique properties to meet specific requirements.
- Consistency and Precision: Automated injection molding machines provide high precision and consistency, ensuring uniformity in production.
- Reduced Waste: The efficiency of the molding process minimizes material waste, making it an environmentally friendly choice.
The Future of Plastic Molding
As technology continues to advance, the future of plastic molding looks promising. Innovations such as 3D printing and smart manufacturing are set to revolutionize the industry. Companies are exploring enhanced materials, like biodegradable plastics, to improve environmental sustainability.
Trends in Plastic Molding Technology
With the rapid growth of technology, several trends are emerging in plastic molding:
- Automation: The integration of robotics and AI in molding processes is increasing efficiency and precision.
- Smart Molding: Smart sensors and data analytics are being utilized to monitor and optimize molding processes in real-time.
- Eco-Friendly Materials: The demand for sustainable materials is growing, leading to the development of new, environmentally friendly options in plastic molding.
- Customization: Advances in technology are enabling more customization in product designs, catering to specific customer needs.
Choosing the Right Plastic Molding Partner
When exploring plastic molding as a manufacturing solution, partnering with the right expert is crucial. Here are some factors to consider when selecting a plastic molding partner:
- Experience: Look for a company with a proven track record in the industry and expertise in various molding techniques.
- Capabilities: Ensure the partner can handle your specific molding requirements, including material types and production volumes.
- Technology: A good partner should leverage modern technology to enhance production efficiency and precision.
- Quality Assurance: The company should have strict quality control measures in place to deliver consistent, high-quality products.
- Customer Service: Strong communication and support are vital for a successful partnership, ensuring your needs are met promptly.
Conclusion
In conclusion, plastic molding is a vital component of modern manufacturing, providing numerous benefits across various industries. Understanding the different types of molding processes, their advantages, and the future trends in the industry is essential for businesses looking to leverage this powerful technique.
Whether you are involved in automotive, consumer goods, electronics, or medical applications, the significance of plastic molding cannot be overstated. As we move forward, embracing innovation and sustainability in plastic molding will be key to maintaining competitiveness and meeting the evolving needs of consumers.
For businesses in the field, collaborating with a reliable partner like DeepMould.net can provide the expertise needed to navigate the intricacies of plastic molding, ensuring efficient production and quality results.