CNC Mold Making Factory: Innovating Precision Manufacturing
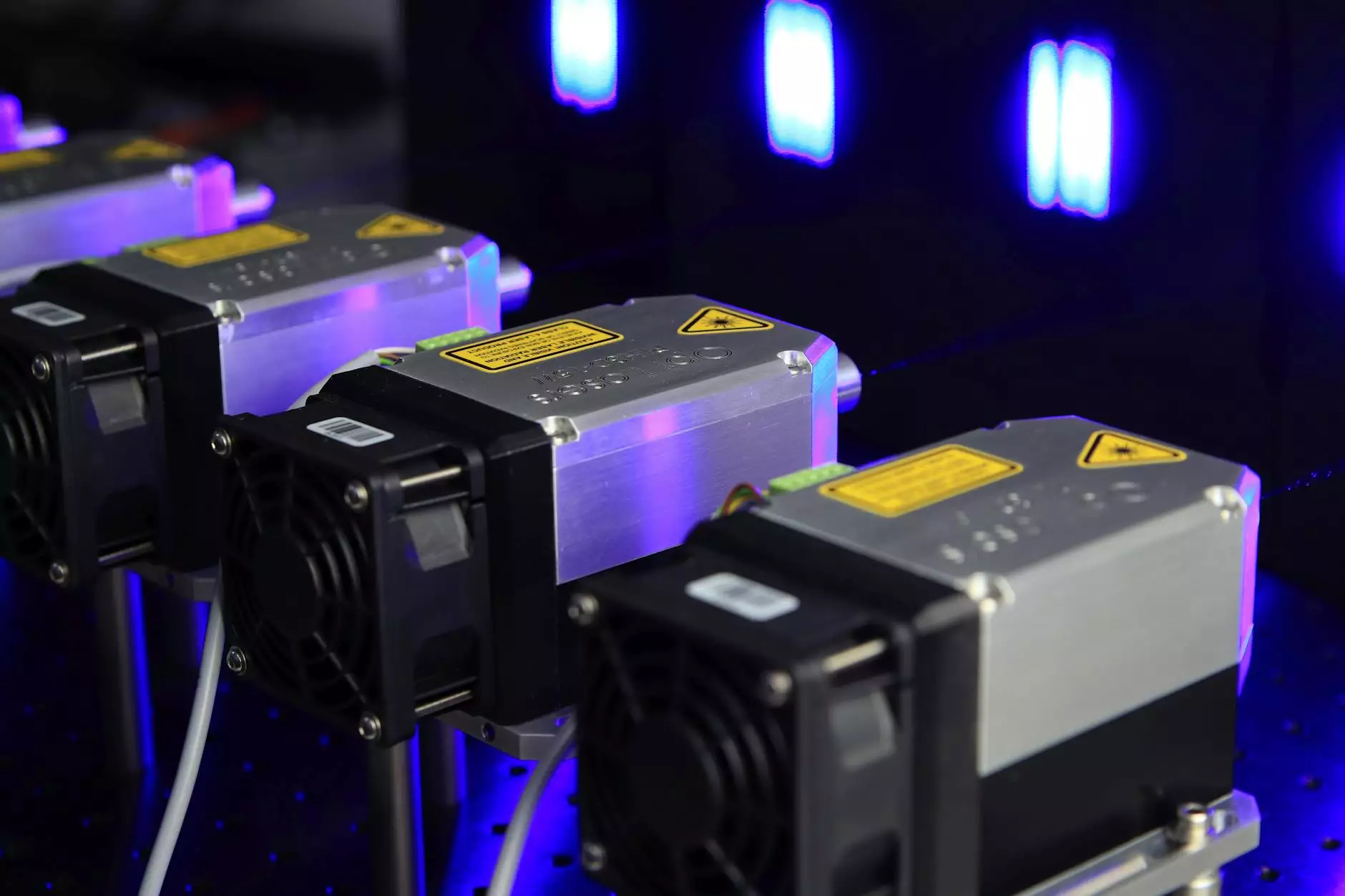
In today’s competitive industrial landscape, the role of a CNC mold making factory is more critical than ever. As businesses strive to improve efficiency and reduce production costs, advanced manufacturing technologies have become essential. In this article, we will delve deep into the various facets of CNC mold making, the technologies involved, and how businesses can leverage these capabilities to enhance their operations and profitability.
Understanding CNC Mold Making
CNC mold making involves the use of Computer Numerical Control (CNC) machinery to create precise molds for a variety of manufacturing applications. The process begins with a digital design, which is then translated into machine commands that control the movement of cutting tools to shape materials. This method of mold making allows for unparalleled accuracy, efficiency, and repeatability.
The Importance of CNC in Modern Manufacturing
The integration of CNC technology into mold making has revolutionized the manufacturing industry. Here are some of the key benefits:
- Precision: CNC machines can create incredibly precise molds, essential for high-quality production.
- Efficiency: CNC operations are faster than traditional methods, reducing lead times and increasing output.
- Cost-Effectiveness: Although the initial investment in CNC technology can be high, the long-term savings on labor and materials make it cost-effective.
- Flexibility: CNC mold making can be adapted for a wide range of materials and designs, making it suitable for diverse industries.
Key Technologies in CNC Mold Making
The process of mold making in a CNC mold making factory utilizes various technologies:
1. Machining
Machining is the foundational process in CNC mold making. It involves the removal of material from a workpiece to achieve the desired shape and tolerance. Several types of machining processes are employed:
- Milling: Involves the use of rotating cutting tools to remove material.
- Turning: A method that rotates the workpiece against a cutting tool to shape cylindrical objects.
- Drilling: Creates holes in materials with high precision.
2. Laser Cutting
Laser cutting technology is gaining traction due to its ability to cut intricate designs with high precision. This process utilizes focused laser beams to melt or vaporize material, resulting in clean edges and minimal waste.
3. Welding
In CNC mold making, welding is often required to join different parts of a mold or to repair existing molds. Various welding techniques can be employed, such as:
- MIG Welding: Metal Inert Gas welding, suitable for metals like aluminum and steel.
- TIG Welding: Tungsten Inert Gas welding, known for producing strong and precise welds.
4. Plastic Injection Molding
Plastic injection molding is an essential application of molds produced in a CNC mold making factory. This process allows for the production of complex plastic parts through the injection of molten plastic into the mold. Advantages include:
- High Production Rates: Efficient for mass production.
- Versatility: Applicable to a wide range of plastic materials.
5. Vulcanization
Vulcanization is a chemical process that enhances the durability of rubber and similar materials. Molds made in a CNC mold making factory often require vulcanization to improve the performance of the final products, particularly in automotive and industrial applications.
Industrial Supplies: Supporting the CNC Mold Making Process
The CNC mold making process requires high-quality industrial supplies to ensure that production meets the necessary standards. These supplies can include:
- Cutting Tools: Precision tools are vital for effective machining.
- Measuring Instruments: Tools for measuring mold dimensions to guarantee accuracy.
- Coolants and Lubricants: Essential for maintaining the performance and integrity of CNC machines during operation.
The Role of Quality Assurance in CNC Mold Making
Quality assurance is crucial in the mold making process. Each step must be monitored and controlled to ensure that the final product meets the clients' specifications. This involves:
- Regular Inspections: In-process checks at various stages of production.
- Final Testing: Comprehensive testing of the finished molds before delivery.
- Feedback Loop: Analyzing customer feedback for continuous improvement in processes.
Choosing the Right CNC Mold Making Factory
Selecting the right CNC mold making factory can be a daunting task. Here are several factors to consider:
- Experience: Look for factories that have extensive experience in the industry and a proven track record.
- Technology: Ensure they are utilizing the latest CNC technology for optimal results.
- Customer Service: A factory that prioritizes communication and customer satisfaction is essential.
The Future of CNC Mold Making
The future of the CNC mold making factory industry looks promising, driven by continuous advancements in technology. Key trends to watch for include:
- Automation: Increased automation will enhance efficiency and reduce human error.
- 3D Printing: The integration of additive manufacturing will revolutionize traditional mold making by allowing rapid prototyping and customization.
- Sustainability: As industries focus on reducing their carbon footprint, CNC factories are likely to adopt more sustainable practices and materials.
Conclusion
The CNC mold making factory is a cornerstone of modern manufacturing, playing a pivotal role in ensuring that products are created with the highest standards of precision and efficiency. By leveraging advanced technologies such as machining, laser cutting, welding, plastic injection, and vulcanization, businesses can stay competitive in an ever-evolving industry. As we move forward, the focus on quality, sustainability, and technological innovation will drive the future of mold making and ultimately the manufacturing landscape as a whole.
For businesses looking to partner with a reliable CNC mold making factory, consider choosing one that not only boasts state-of-the-art technology but also values customer relationships and quality assurance. Companies like Sumiparts exemplify these qualities, providing comprehensive solutions across categories such as machining, laser cut, welding, plastic injection, and industrial supplies.
In a world where precision manufacturing is paramount, invest in the right CNC mold making factory to elevate your business and achieve long-term success.